In the quest for efficient and sustainable manufacturing processes, the advent of twin-head technology in powder filling has emerged as a game-changer. This revolutionary approach offers the promise of zero waste and full control, transforming the way we think about powder filling operations.
The twin-head configuration of these automated machines ensures a seamless and rapid filling process. By having two heads working in tandem, the filling time is significantly reduced, boosting productivity and output.
One of the key advantages is the minimization of waste. The precise control mechanisms in twin-head technology ensure that the exact amount of powder is dispensed into each container, eliminating overfilling and spillage. This not only saves resources but also reduces costs associated with material waste and cleanup.
With full control over the filling process, manufacturers can set precise parameters for powder quantity, speed, and consistency. This level of customization allows for seamless integration into diverse production lines and ensures that the final product meets the highest quality standards.
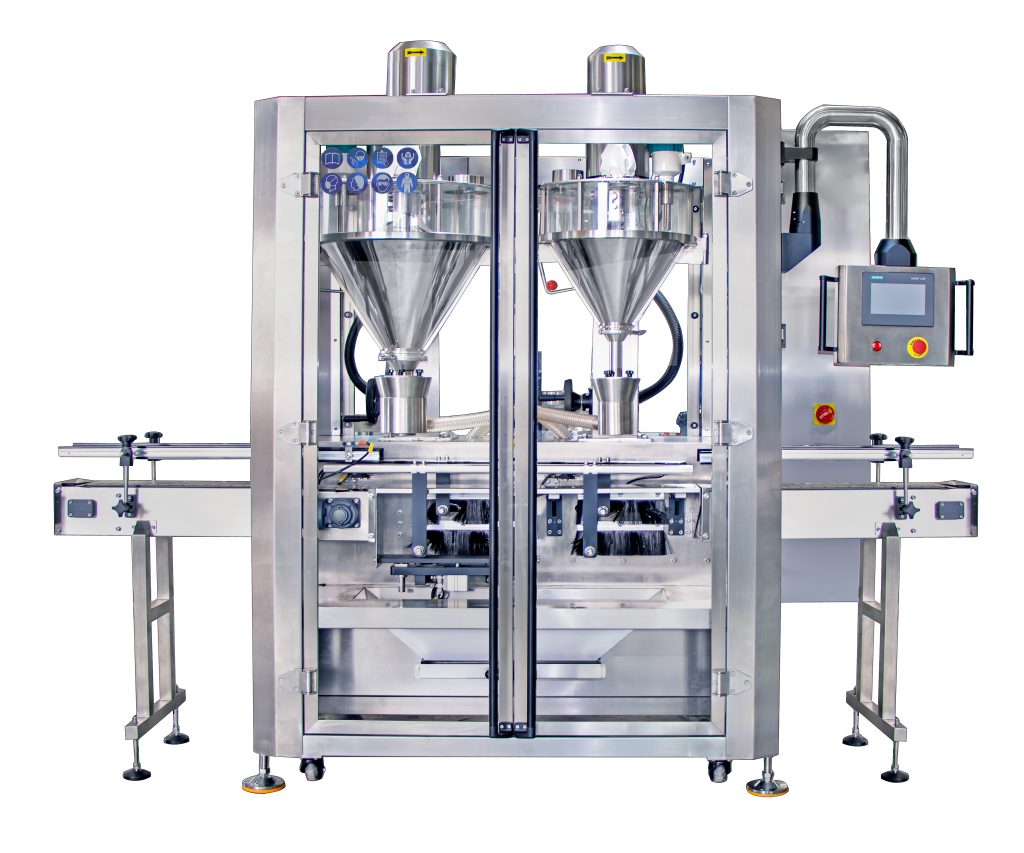
The automation aspect brings consistency and reliability. Every fill is executed with the same level of accuracy, reducing variations and the potential for errors that can occur with manual filling methods.
Furthermore, the twin-head technology helps in maintaining a clean and safe working environment. The controlled filling process reduces dust emissions and the risk of contamination, adhering to strict health and safety regulations.
In conclusion, automating powder filling with twin-head technology offers a compelling solution for achieving zero waste and full control. It represents a significant step forward in the pursuit of efficient, sustainable, and high-quality powder filling operations, setting new standards in the manufacturing industry.