Semi-automatic can seamers can encounter various issues over time. Here are some common problems and their corresponding fixes.
One frequent problem is inconsistent seaming. This could be due to worn-out seaming rollers or incorrect pressure settings. To solve it, replace the worn rollers and adjust the pressure to the appropriate level as specified in the machine manual.
Another issue is jamming of the cans during the seaming process. This might be caused by misaligned components or foreign objects in the machine. Check and realign the parts, and clear any obstructions to ensure smooth can movement.
Leaking seams can occur if the sealing compound is of poor quality or not applied evenly. Use high-quality sealing compound and ensure its even distribution to prevent leaks.
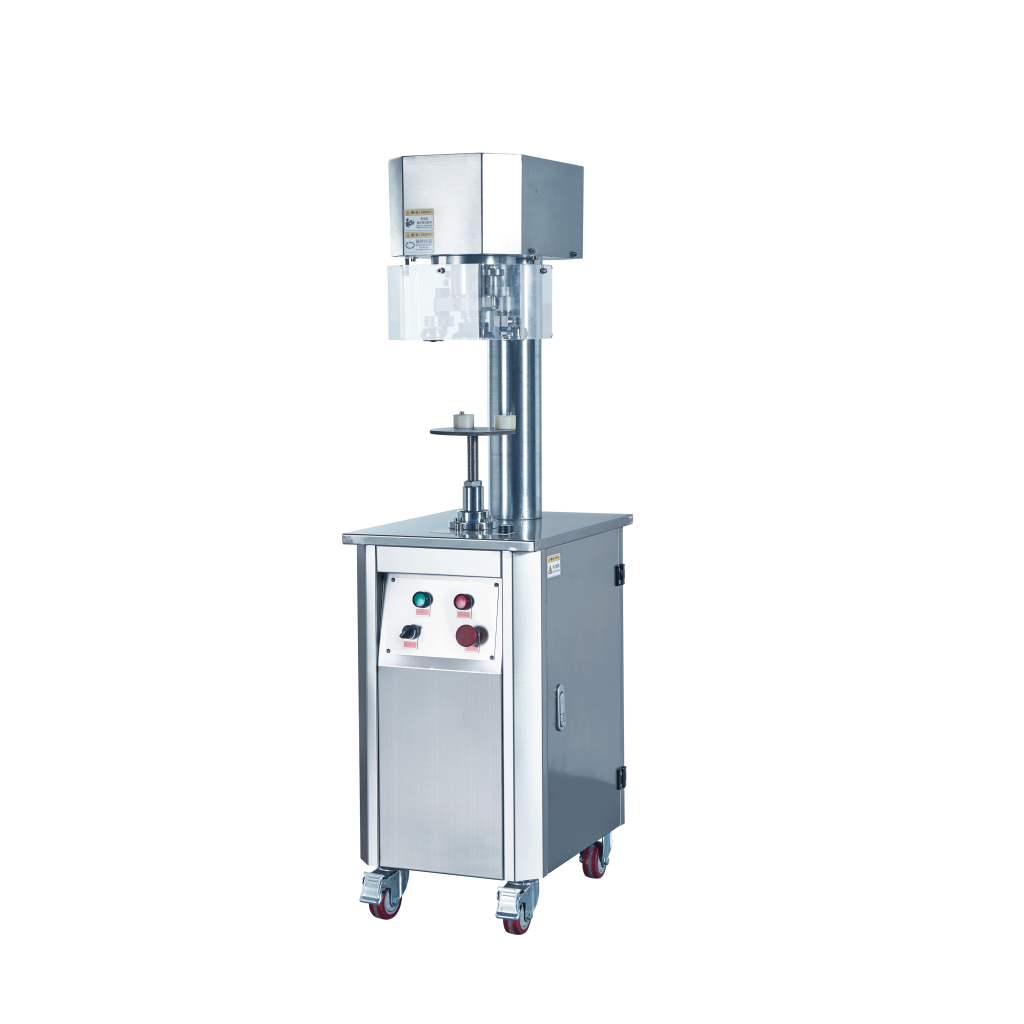
Slow operation of the seamer can be a problem, often resulting from a lack of lubrication or a malfunctioning motor. Regularly lubricate the moving parts and have the motor inspected and repaired if needed.
Inaccurate seaming dimensions could be due to incorrect adjustments or damaged measurement tools. Re-calibrate the machine and replace any damaged measurement devices for precise seaming.
Electrical faults can also arise, such as short circuits or faulty connections. Inspect the electrical wiring and connections, and repair or replace any damaged components.
By being aware of these common problems and knowing how to address them promptly, you can keep your semi-automatic can seamer operating efficiently and minimize production disruptions.