The semi automatic glass bottle vacuum capping machine operates on a fascinating and precise working principle that ensures efficient and secure capping of glass bottles.
The process begins with the placement of the glass bottle onto the machine’s platform. The bottle is held firmly in position to prevent any movement during the capping operation.
Next, a vacuum is created inside the bottle. This vacuum is crucial as it helps remove any air present and creates a low-pressure environment.
The cap is then placed on the bottle’s mouth. The machine’s mechanism applies pressure to the cap while maintaining the vacuum. This pressure, combined with the vacuum, ensures a tight and secure seal.
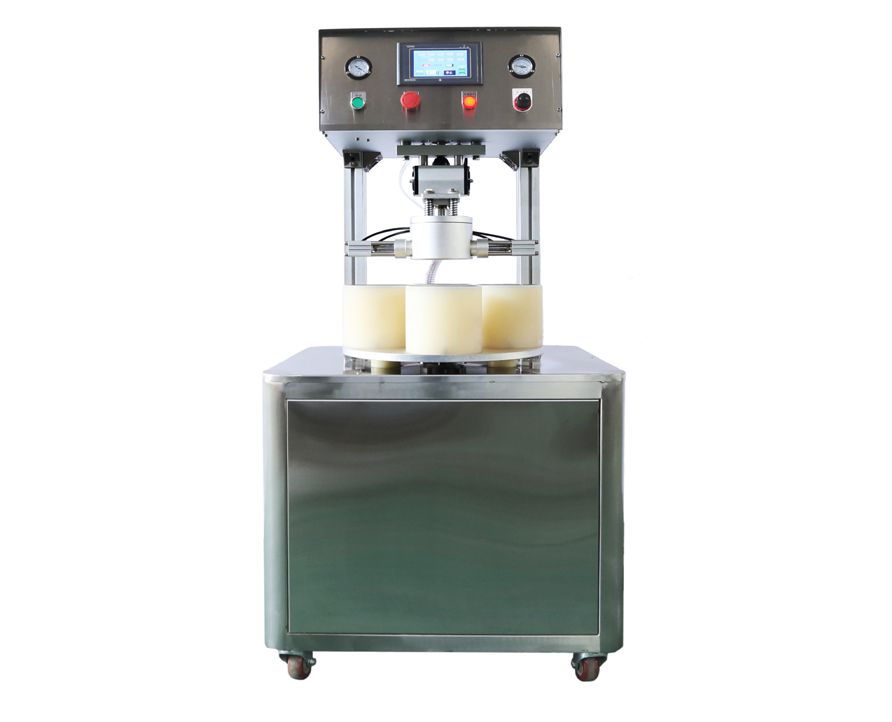
The semi-automatic aspect of the machine means that while some steps are automated, human intervention is still required at certain points. For example, the operator might need to load the bottles and caps onto the machine and initiate the capping process.
The control system of the machine regulates the vacuum level, pressure applied, and the duration of the capping operation to achieve consistent and high-quality seals.
Sensors and detectors are incorporated to monitor the process and ensure that each capping operation meets the specified standards. If any deviations or errors occur, the machine alerts the operator or stops the process to prevent faulty capping.
In summary, the working principle of the semi automatic glass bottle vacuum capping machine relies on the creation of a vacuum, precise application of pressure, and controlled operations to provide reliable and effective capping for glass bottles. Understanding this principle helps in the efficient operation and maintenance of the machine, as well as in achieving optimal packaging results.