Vacuum Nitrogen Flushing Can Seaming Machines have become indispensable in the packaging industry, offering superior protection and preservation for various products. This guide will take you through the essential aspects of these machines.
First and foremost, let’s understand the working principle. These machines operate by creating a vacuum inside the can to remove air and then flushing it with nitrogen. This process helps to extend the shelf life of the contents by minimizing oxidation and spoilage.
The components of a vacuum nitrogen flushing can seaming machine are crucial. The vacuum pump is responsible for generating the necessary vacuum, while the nitrogen injection system ensures precise and controlled introduction of the gas. The seaming head is designed to create a secure and leak-proof seal.
When choosing a machine, several factors come into play. The production capacity should align with your business needs. Consider the size and type of cans it can handle, as well as its adjustability for different can specifications. The quality and durability of the machine’s construction are also vital for long-term reliable operation.
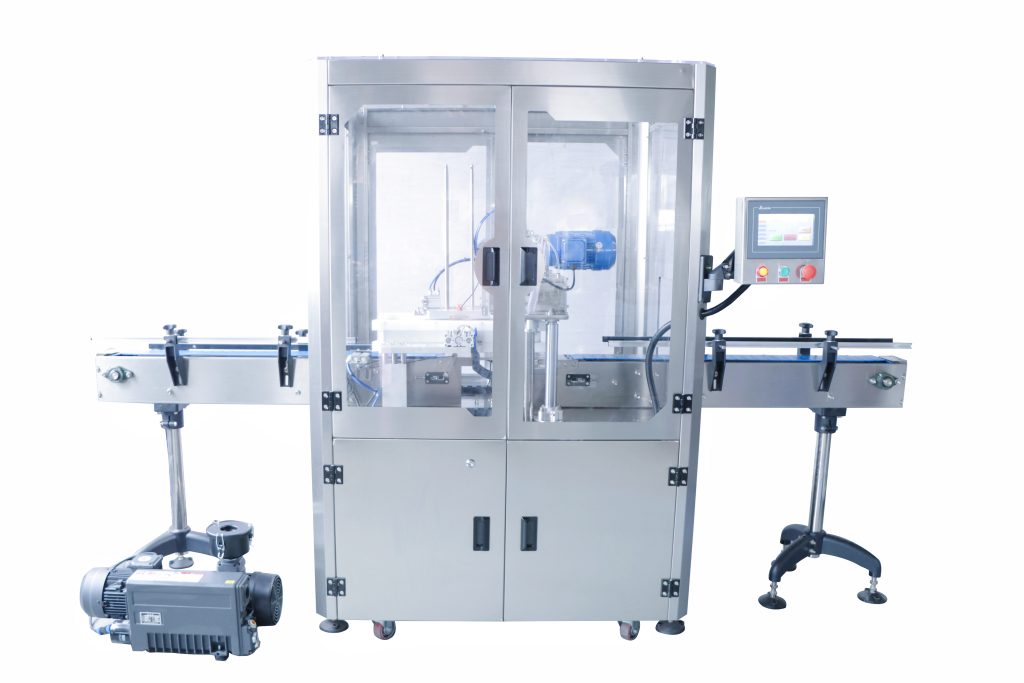
Maintenance is an important aspect to keep the machine running smoothly. Regular checks of seals, pumps, and other components, along with proper cleaning and lubrication, can prevent breakdowns and ensure consistent performance.
The latest advancements in technology have brought improvements such as enhanced control systems for more precise operations, energy-efficient designs to reduce operational costs, and integration with other packaging equipment for seamless production lines.
In conclusion, understanding the workings, components, selection criteria, maintenance requirements, and technological advancements of Vacuum Nitrogen Flushing Can Seaming Machines is essential for making informed decisions and optimizing your packaging processes.